Ao montar um projeto de expansão da planta ou avaliar as causas da ineficiência de um setor, muitas alternativas são levantadas e algumas colocadas em testes. O uso de softwares de simulação, com a interpretação correta dos dados podem oferecer soluções para determinadas demandas antes da tomada de decisão em novos investimentos.
Em uma indústria de autopeças, a linha de produção de virabrequins não estava atingindo as metas estabelecidas. Os especialistas e gestores daquele setor já haviam notado há algum tempo a existência de um gargalo na produção, especialmente no primeiro pórtico, estrutura que fica sobre um grupo de equipamentos e possibilita a movimentação de transportadores aéreos sobre seus trilhos.
A avaliação dos técnicos da empresa, após algumas reuniões, foi de que existiam muitas variáveis envolvidas no processo e que seria difícil apontar uma solução sem testes. Antes de realizar a compra de qualquer equipamento, a empresa decidiu contratar uma empresa de consultoria para que, através de simulações das hipóteses encontradas, pudessem solucionar o problema e aumentar a eficiência naquela etapa em 5%. Seria preciso considerar envolvendo as falhas dos equipamentos, os tempos de ciclo da máquina, a distribuição dos operadores para reparo durante as falhas e vida útil das ferramentas.
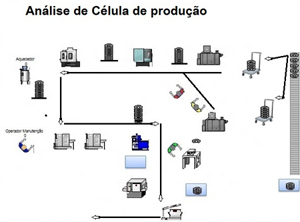
Como a empresa já possui um sistema supervisório armazenamento de dados do processo produtivo, o tempo de coleta foi reduzido e todo o trabalho, com a apresentação de três soluções diferentes foi realizado em quatro semanas. “O trabalho de validação dos dados e modelagem é que toma o maior tempo no nosso trabalho. Mesmo quando a empresa utilizada supervisórios, como foi o caso nessa indústria, os dados não estão prontos para uso e é preciso fazer uma “limpeza” para utilizá-los corretamente. Depois disso, ainda há a validação com o cliente, para conferir se os dados enviados ao software correspondem à realidade e gerar confiança no trabalho realizado”, explica o engenheiro de produção e diretor da empresa
Linecon, Alexandre Betiatto.
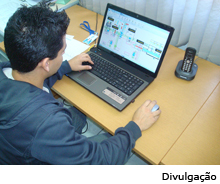
A primeira suposição da gerência, era a de que a estrutura da célula composta por cinco máquinas de comando numérico (CNC) – dois centros de usinagem e três tornos – deveria comportar mais um torno. Durante os trabalhos de simulação de modelagem foi constatado que o problema estava nas constantes paradas para trocas de ferramenta. Uma das soluções apresentadas pela Linecon foi a adoção de ferramentas com uma maior vida útil, o que aumentaria a eficiência da linha em 5,3%, mas o custo das novas ferramentas seria muito alto.
Outras análises foram realizadas e então foi percebido que o tempo de parada de máquinas para manutenção estava além do considerado normal. Em alguns momentos as máquinas quebravam simultaneamente e como havia apenas um operador disponível para aquela máquina, uma ficava um longo tempo aguardando ser atendida. A alternativa levada ao simulador foi o treinamento dos operadores de forma que todos estivessem aptos a consertar todas as máquinas do setor. O resultado deste último cenário foi um aumento na produção mensal de 1673 peças para 1802, um aumento de eficiência de 7,7%. As simulações mostraram um novo método de trabalho para os operadores, dispensando a necessidade de compra de maquinário e novas ferramentas.