Uma nova pesquisa, realizada pelo Institut für Kraftfahrzeuge (ou, em português, Instituto para Veículos Motorizados) da Universidade de Aachen, na Alemanha, põe fim a uma dúvida frequente nas áreas de projeto, inovação e especificação de materiais em montadoras ao redor do mundo: qual o material mais efetivo na diminuição da massa de veículos? O alumínio ou o aço de alta resistência?
Segundo o estudo, concluído em maio desse ano, a resposta é inquestionável: enquanto as ligas de alumínio (com limite de escoamento em torno de 400 MPa) oferece potencial de redução de peso de até 40% para os principais componentes automotivos, os aços de alta resistência (com limite de escoamento de até 1.200 MPa) garantem apenas 11% de diminuição.
Para chegar a esse resultado, os pesquisadores se valeram de análises e simulações numéricas quantitativas por meio das quais avaliaram o potencial máximo de aplicação de cada um dos metais na fabricação do conjunto estrutural e painéis de fechamento (BIW – Body in White) de um carro. Isto, sem comprometimento da segurança e do desempenho estrutural do veículo. Como referência, usaram um modelo compacto 2006, com peso total de aproximadamente 1,26 mil kg. Definidas as aplicações, os pesquisadores mediram os limites da redução de peso potencial de cada um dos materiais.
“A pesquisa lançou a seguinte questão: quanto peso é possível reduzir de um veículo usando aço de alta resistência ou alumínio onde for possível e considerando, principalmente, as limitações de resistência e rigidez de ambos os materiais?”, explica Randall Scheps, presidente do grupo de transportes da Aluminium Association - The Aluminum Association’s Auto & Light Truck Group.
O estudo constatou que o uso do alumínio pode resultar em reduções de peso por componente entre 14 e 49%, como apresentado no gráfico abaixo. De acordo com a pesquisa, “em componentes em que a rigidez é relevante e dependendo do formato da peça e das cargas envolvidas, o alumínio torna possível a redução de mais de 50% do peso em comparação com componentes similares em aço”.
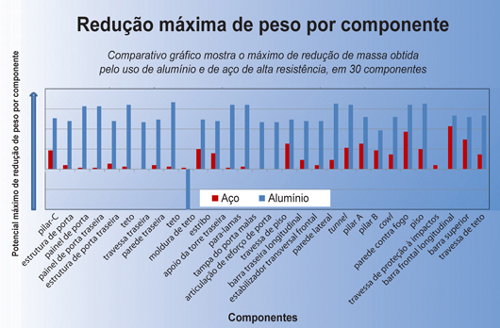
No conjunto, os números conclusivos mostram que a carroceria de um monobloco com máximo aproveitamento de alumínio não ultrapassa 228 kg. “Considerando a economia indireta de massa – proporcionada pelo uso intensivo de alumínio, que garante diminuição de peso e volume dos sistemas powertrain, freios etc. – os 228 kg de alumínio reduzem a massa do BIW em 129,5 kg, se o alumínio estiver substituindo o aço de alta resistência”, explica Scheps, que conclui: “De fato, o alumínio é o caminho para alcançar grande quantidade de redução de peso”.
A definição dos critérios para especificação das aplicações de aço de alta resistência e de alumínio em partes da carroceria considerou a relevância da resistência e da rigidez de 26 componentes (que podem, cada um, consistir de uma ou mais peças) do monobloco-referência em situações de choque e colisões. Esses componentes foram submetidos a testes extensos de impactos laterais, frontais e dianteiros – com cargas variáveis –, bem como a análise de torção estática global, flexão estática máxima, formabilidade, elasticidade, união, flambagem, entre outras.
As análises numéricas mostraram que cerca de 38% dos componentes da carroceria de um veículo são altamente relevantes para a rigidez global do automóvel, mas têm baixa relevância quanto à resistência, em colisões/acidentes. Para esses elementos, o uso de aço de alta resistência se mostrou impróprio. O motivo é que esses aços, por serem mais resistentes, permitem a construção de peças mais finas – logo, mais leves; porém, em quase 40% das peças analisadas, foi constatada a impossibilidade de redução da espessura das paredes sob o risco de comprometimento da rigidez. Já o alumínio garante redução de peso sem comprometer a rigidez.
“Há aplicações que precisam de resistência e outras que precisam de rigidez. O aço de alta resistência é adequado às peças que demandam resistência, mas não se mostrou seguro aplicar o material em todas as peças e em todos os componentes devido às exigências desses elementos em termos de rigidez“, conta Scheps, que ressalta: “Outro dado relevante comprovado pela pesquisa é que para a maioria dos componentes estruturais, a resistência não é fator limitante para a substituição do alumínio por aço”.
Para conferir a íntegra do estudo, acesse: http://www.eaa.net/en/applications/automotive/studies
Gostou? Então compartilhe: